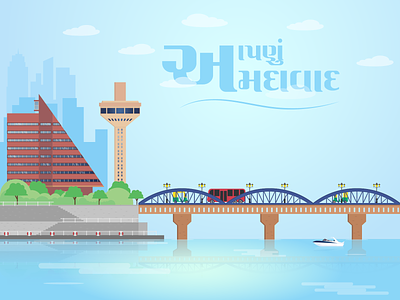
Following a Semiconductor Supply Chain Summit organised on November 14 in Taipei, DIGITIMES Research analyst and project manager Eric Chen said it would take India 10 years to establish a mature 28nm process. He identified the challenges posed by equipment, workforce, and ecosystem requirements. However, US-based Fab Economics—a boutique semiconductor Fab/ATMP greenfield projects advisory and implementation practice firm—has rebutted these claims. Fab Economics CEO Danish Faruqui in an exclusive interview with Business Today estimates a timeline of 3.2 years for India’s first production-ready 28nm Fab. Edited excerpts:
BT: Do you agree with the claim that India would require a realistic timeline of about 10 years to have the first production-ready 28nm fab?
Danish Faruqui: We definitely do not agree to the 10-year timeline. If that happens, it will be the slowest semiconductor project in history, leading to all partners of semiconductor development in India across the value chain and materials and equipment supply chains falling apart and striking out India as a destination for mature node manufacturing and packaging.
Our firm view is that India can definitely deliver the first production-ready 28nm fab with best-in-class benchmarks provided success factors across policy, process, people, systems, and technology transfer are met—which are doable, and the India Semiconductor Mission is on the right path at the right pace to enable and enforce such success factors for players foraying to set up semiconductor sites in India.
We at Fab Economics have granularly estimated the timeline for a model production-ready 28nm fab in India across all stages, i.e., subfab construction, fab construction, fab facilitation, fab equipping, equipment quals / line quals, site-level technology transfer, site certifications for major 28nm end markets, fab productisation (NPD, NPI, CS), fab production-ready certification with full loop 28nm silicon and high volume manufacturing onset. Our estimate for a production-ready 28nm fab in India is around 3.2 years, provided there is parallel enablement of success factors at each stage, which is definitely possible with the right strategy, planning, and implementation at the site level. We see no reason why India cannot replicate benchmarks and success for 28nm as seen across multiple sites in Asia, including China, Taiwan, and Germany.
To illustrate, Bosch and Infineon from Germany, NXP from the Netherlands, and TSMC from Taiwan have come together to form JSMC for a 28/22 nm and future 16/14nm fab in Germany with a production-ready target within 3 years from the start.
Specifically in China, multiple 28nm Fab’s have been completed between 2021 and 2024 (3 years), and as per Fab Economics Research and Analysis, China’s 28nm capacity will increase by over 38% from 2021 to 2024, which happens to be the node with the most capacity expansion in China due to the heavy reliance and imminent transition of various end markets on 28 nm including automotive, industrial, and consumer electronics.
Instead, we want to pose a reverse question: When China, Taiwan, and Germany can do it within 3 years, why can’t India?
In fact, based on Fab Economics proprietary Fab site-level multiyear economic modelling across all CAPEX and OPEX cost structures, it is estimated that a 28mn Fab in India will have a lower total cost of ownership than many competing world regions. To bring a case in point on a specific aspect in favour of India that has implications both on schedule and cost metrics, for almost a year, the Intel proposed factory in Magdeburg, Germany, has been hit by multiple schedule delays. A prominent reason was high electricity prices, resulting in substantially high Opex cost structures at site level during the construction and operations phases.
such that factory economics or fab-level economics cannot compete with the rest of the world (fab economics dictates metrics like COGS), and thus Intel requires additional subsidies to compensate for a decadal operations cost penalty that runs in billions of dollars.
As per our exclusive insights, Intel’s site in Magdeburg, Germany, had an electricity price of 50 cents per KWh, which is 15 times more costly than the price.
across Indian states when aggregated across all types of Fab operations requirements. Thus, India has many USP’s as well when it comes to greenfield fab and ATMP projects. However, it is also true that many of such USP’s, as aforestated, have not been marketed to the world so far.
Lastly, we are particularly amazed by the high priority focus and relentless pursuit by the Indian government in the strategic area of semiconductors, including the PM himself forging the Micron investment in India. In a very short period of time, India has managed to forge strategic alliances for semiconductor collaborations with multiple nations’ leading semi-value chains, including the US, EU, Japan, and Taiwan.
Business Today: Do you agree with the claim that India achieving semiconductor self-reliance at the 28nm level in India in a decade is a reasonable and promising goal for India?
Danish Faruqui: We think this is an extremely low bar setting for India to have a decadal goal of just self-reliance at 28nm and deprecates all that India brings to bear for semiconductor ecosystem development. India has been making steady strides across Si-based logic, memory, analogue fabs, compound semiconductor fabs, display fabs, and associate ATMP/OSAT facilities via the latest PLI schemes.
tailored for each area apart from its existing thriving Design Ecosystem, all of which indeed represent a holistic approach towards semiconductor self-sufficiency adopted by India for various domestic markets—no one can deny it.
India is offering one of the most competitive subsidy and incentive support packages across centre and state levels for a diverse portfolio of semiconductor manufacturing and packaging sites, all aligned to the various end market demands associated with growing India. The high priority allocated by the Government of India to ISM is commendable and happening for the first time in India. We from the semiconductor industry have long awaited such formidable and bold semiconductor commitments from India.
In addition, like the US, India too has taken a product-level on-shoring approach, i.e., design, manufacturing, assembly, testing, and packaging, to deliver a trusted value chain within the country for economic competitiveness and national security.
Based on our exclusive Demand and Consumption datasets developed for India, we forecast that India, with adequate partner support and enablement of required success factors, could become self-sufficient across multiple Si-based mature node processing in the next 6 years and become a wafer-level and product-level (via ATMP facilities) major exporter to the world within 10 years. That’s the bar we would like India to meet and exceed.
Of course, there are other areas across the semiconductor ecosystem—compound semi, display value chain, and material supply chains—where we have practical roadmap forecasts.
All in all, India is way beyond just 28nm self-sufficiency in 10 years. India is off to a great start with a very competitive semiconductor policy and strong commitment and support from the government to transform India into a semiconductor manufacturing hub.