What does it take to be one of the World Economic Forum’s (WEF) most digitally advanced Lighthouse factories?
The WEF Global Lighthouse Network recognises factories that incorporate Fourth Industrial Revolution technologies (4IR) such as artificial intelligence and big data analysis to maximise efficiency and drive sustainable growth, while upskilling their workforce and protecting the environment.
For the team at our Sonepat Nutrition site, this means leveraging technology, teamwork and partnerships to power growth and productivity.
“We are building factories of the future by integrating advanced digital technologies across our end-to-end operations, while sustainably reducing our environmental footprint,” explains Reginaldo Ecclissato, Unilever Chief Business Operations and Supply Chain Officer.
“We do so not just to meet increasing consumer demand and drive superior business growth but also to upskill and equip our teams for the future of work.”
Building our factories of the future
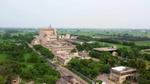
As Unilever’s largest manufacturing site for Horlicks, Sonepat’s 4IR journey began in 2020 when it was brought into Unilever’s manufacturing family.
Fast forward a few years, and the results speak for themselves. Service levels have improved by 18%. Factory conversion costs have reduced by 40%.
Real-time monitoring and precision control have also reduced food waste by 30% and forecasting accuracy has seen significant improvement.
Results that reflect ambitious growth ambitions
Better yet, 4IR technology is catalysing progress in achieving Unilever’s ambitious plans for growth, including:
Superior product quality: An 86% reduction in product defects has been achieved in part through the implementation of ‘lights off’ manufacturing. This is a process where production operations are automated and managed with minimal human intervention, thanks to advanced real-time data capturing and decision-making.
Efficiency optimisation: Factory process efficacy has been assured by the introduction of multiple digital twins (a virtual replica of the system it is modelled after) that can monitor, analyse and ultimately suggest optimised operational parameters that can then be delivered to the live system with no interruption to operations.
Supply agility: The factory’s planning accuracy has been boosted by cognitive decision-making technology which ensures that production, distribution and procurement signals are optimised to match market needs. So far, this unique application is serving diverse geographic regions across India.
Environmental sustainability: Sustainably sourced biofuels, combined with the introduction of a boiler digital twin that optimises the efficacy of the real-world boiler including its energy use, have successfully reduced the factory’s Scope 1 greenhouse gas emissions by 88%, while also providing local farmers with a profitable use for their agricultural waste. (Scope 1 emissions are those produced directly by Unilever from sources we control or own.)
How we’re upskilling our teams as well as our technology
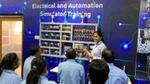
“This recognition (as a WEF Lighthouse factory) could not have gone to a more deserving team,” says Jennifer Han, Unilever Chief Product Supply Chain Officer for Nutrition.
“Since starting their digitalisation journey three years ago, they have seamlessly upscaled advanced technology in their operations to become one of the leading factories of the future in our Nutrition business.”
Abhishek Jain, Factory Director at Sonepat, agrees, adding that upgrades of this scale can only really work if they go hand in hand with equally robust team training.
At Sonepat, for example, 100% of the team successfully completed an extensive upskilling programme.
“70% of the learning at our factory happened on the job, 20% through mentoring and coaching and 10% in the classroom,” he says, adding that this included safety focused modules using artificial intelligence and augmented virtual reality HoloLens technology.
The power of partnerships
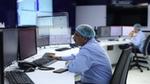
For Yogesh Mishra, Executive Director, Supply Chain HUL & Head of Supply Chain, South Asia, however, there is one more key component to Sonepat’s digital success story, and in particular to the speed at which it was developed.
“Strategic collaboration with technology providers was critical in ensuring that tech fits the requirements of the factory,” he says.
“By creating squads that included Unilever colleagues, infrastructure suppliers and partners, we were able to ensure a faster roll-out of digital innovations.”
Next steps
To be named a WEF Lighthouse Factory is one of the highest accolades in the field of advanced manufacturing, and for Yogesh this recognition confirms the need to continue to integrate 4IR technologies into our end-to-end value chain.
“Digital transformation will continue to be an integral priority across our end-to-end manufacturing operations in Hindustan Unilever and across South Asia,” says. “To drive consistent, competitive, profitable and responsible growth, we must adopt advanced technology in our operations at scale.”